
Whatever you use needs to be sealable, disposable and you'll want a few of them. You'll need some containers to mix stuff in. While you are there, get one of those long-handled, angle-head, cheap, nook-and-cranny paintbrushes. If you can find some that look like they've been on the shelf since Noah made landfall, get those and don't move them more than you need to. I'd then go to the nearest Screwfix, Toolstation, B&Q, etc and buy 2 or 3 x 2 kg kg tubs of cheap fire cement. The body-soluble stuff can be found by the metre on ebay. You'll want 25mm thick, 128 kg/m3 (1" thick, 8 lb/cu.ft). I'd buy some extra blanket: enough for a couple of reline jobs on the forge you have. You'll need a fair bit of actual forging under your belt before you are in a position to decide exactly what sort of work you are going to need to build it for.įrom the OP, it doesn't sound like you'll need welding temperatures for a while yet (" does this seem adequate to heat and shape metal with?") My advice is to accept that you are not going to build a forge-for-life anytime soon. The body-soluble stuff is only rated to 1200 degC as a rule.
#What does forged in fire do with the meat full
The blanket is relatively easy to get in "our" quantities, though it's become difficult to find anything less than a full roll of the 1400 degC (2600 degF) stuff since the body-soluble fibre started to become popular. The same tends to be true of Mizzou and most other hard castable refractories.
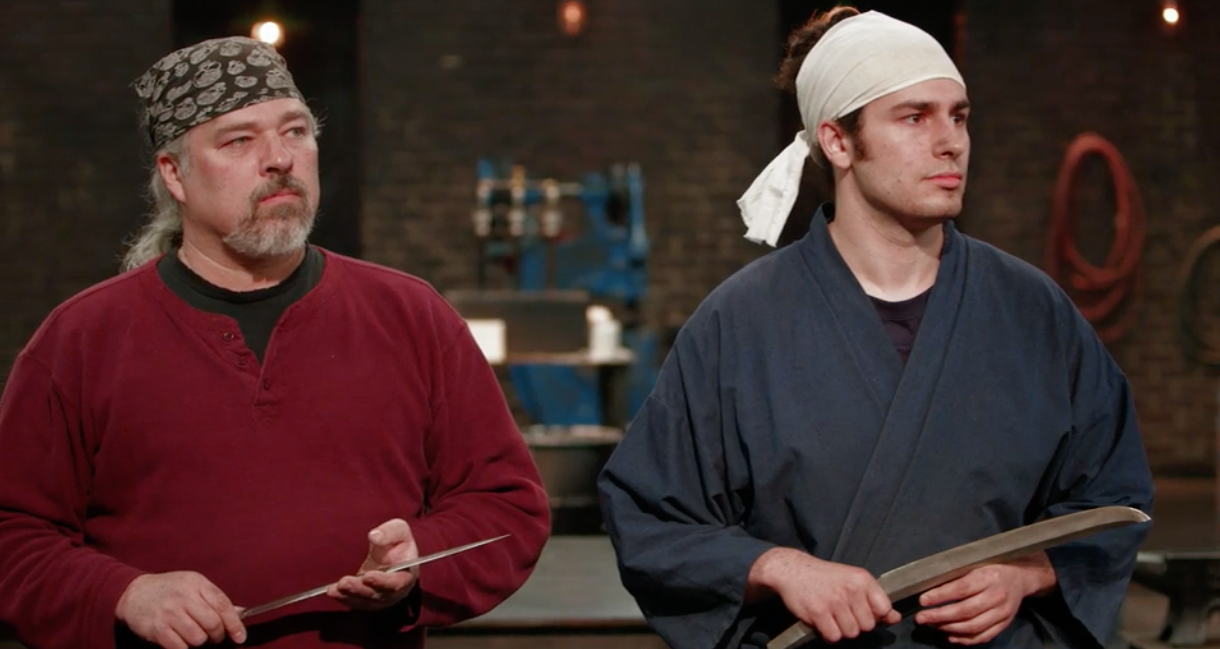
I gather Kast-O-Lite 30 is very highly thought of, but it's not very easy to get hold of here, particularly in small quantities. Refractory coatings are not particularly easy to give good advice on, at least over here. If you burn X gas per hour at 30 PSI, you'll burn 0.707X at 15 PSI, 0.5X at 7.5 PSI, 0.25X at just under 2 PSI and about 0.18x at 1 PSI. For a given gas jet, gas flow varies with the square root of pressure. Operating pressures are likely to fall in the 0-0.2 MPa range (0-30 PSI). I still need to try it in a "normal" forge to see if it'll get to welding temperatures and it's something to get around to in the next few weeks: I prefer to do in the dark so that I can see what the flames are doing and it is best done in the the dark winter evenings. I only did my initial testing in a purpose-designed Heat-Treat forge, so I've not tried for maximum temperature yet. Mine seems to get hotter as the choke is opened while remaining on the fuel-rich side of stoichiometric even with the choke fully open. It seems they've got the gas jet (which looks to be a drilled hole) about right, IMO. I bought a DFP burner only off ebay, just to see whether they'd done a good job of it and I was impressed.

If you've run with the choke closed, that'll explain the sooting. The second is the flame temperature and this is adjusted by varying the choke position (the disc on the back of the burner that screws up and down to vary the air gap between the bellmouth and the disc).

The first is the amount of gas being burned and this is controlled by adjusting the gas pressure. I can't see the end of the burner where adjustments are made, so it's not clear whether it's a DFP or a DFPProf burner. So, why right now? Because every time you heat the forge, that insulation takes a set, and that means that if you wait to move the floor, the forge will end up with two permanent creases in the wall, where you don't want them. Why? Becuase otherwise your insulation will not last very long. Yes, that means you will have to move the legs too. You must move the half brick floor clockwise until the flame impinges on it toward its near edge, rather than on the forge wall. This brings up the very first thing you must do before going any further. This means that at the very least you will have to turn the forge up hot enough to burn away all traces of this chemical, and the carbon it is leaving on your insulation before you can either rigidize the ceramic blanket or seal coat it. Something in the insulation is cooking off. Your forge photo shows an excellent flame coming from its burner, which is a problem for you the reason is that such a flame is not causing the carbon build up on your insulation.
